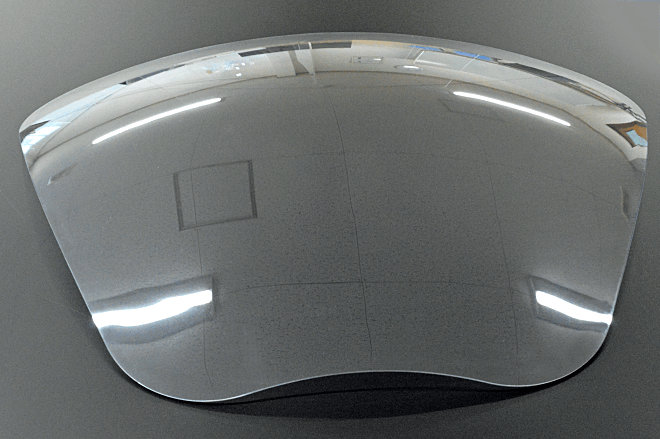
シート(樹脂板)成形とは?シート成形の種類を徹底解説!
私たちの身の回りには、樹脂で作られた製品があふれています。これらの製品の多くは、「シート成形」という技術によって形作られています。 シート(樹脂板)成形とは? 「シート成形」とは、...
真空成形とは、熱を加えることにより、熱可塑性のプラスチックシートを軟化させた後に、真空によりシートを成形型に密着させて一定形状に成形する加工方法です。また、真空成形後にプラスチックシートを冷却して固化させ、後工程で余分な部分を切断する(トリミング)ことで、製品が完成します。
射出成形とよく比較されることがある工法ですが、真空成形では凹または凸のどちらかのみの型でよいため型費用が安価となる、成形型の製作期間が短い、など様々なメリットがあります。
一方で、真空成形は、上述の加工方法の特性上、設計時には注意するべき点が多々あります。そこで、当記事では、真空成形品の設計で失敗しないための7つのポイントをご紹介します。真空成形の採用を検討されている方は、ぜひ参考にしてください。
真空成形は材料がシート形状であるため、成形できる製品の厚みは、一般的に1mm~5mm程度です。これより薄すぎると強度が不足し、厚すぎると成形が困難となります。設計の際は、製品に必要な強度と成形性を考慮して、適切な厚みを設定しましょう。
真空成形品には、抜き勾配を設ける必要があります。抜き勾配とは、成形品を金型からスムーズに抜き取るために、製品の側面に付ける傾斜のことです。抜き勾配がないと、成形品が金型に引っかかって破損したり、傷がついたりする可能性があります。
抜き勾配が大きければ大きいほど、厚みムラが減り外観が良くなるため、用途上、許容できるのであれば、抜き勾配は大きくとった方が良いといえます。
真空成形はシート形状の材料を引き延ばす加工方法であるため、極端にエッジある形状を成形すると、製品厚みのムラやドラッグラインが大きくなる恐れがあります。そのため、これらを防止するため、エッジのある形状は極力避け、可能であれば角部はR形状にすることを推奨します。
真空成形では、凸型(雄型)と凹型(雌型)の片側の金型を用いて、成形を行います。そのため、予め、意匠面(製品の表面)をどちらであるか、どちらの面に寸法精度が求められるか、を考慮した上で凸型・凹型のどちらが最適か検討する必要があります。
ちなみに、凸型と凹型のどちらの金型を使うかで、成形型のコストが変動します。一般的に、凸型の方が金型が小さくて済むため、安価な傾向があります。一方、凹型は金型が大きくなるため、高価になる傾向があります。
射出成形等では、ボス形状を一体成形することが可能です。しかしながら、真空成形ではボス形状を一体成形することはできません。そのため、成形後に、別部品として製作したボスを接着する方法を推奨します。
例えば、真空成形品の厚みが2mmなどと薄い場合、製品の剛性が弱まるケースがあります。このような場合、剛性を強めるために、段や溝をつけることが重要です。
真空成形では、加工方法の特性上、どうしても成形時にドラッグラインが発生したり、取り扱い時に傷がつくことがあります。これらの傷やドラッグラインなどを目立たせたくない場合は、①シボ目を大きくする、②材料の色を明るくする、などの工夫が必要です。
いかがでしょうか。今回は、真空成形品の設計で失敗しないための7つの注意点についてお伝えしました。
三栄プラテックでは、樹脂の真空成形・圧空成形・熱プレス成形・R曲げ加工から切削・溶接・組立まで一貫して対応しております。当社にお任せいただければ、高品質な真空成形品を納入させていただきます。実際にこれまでも、外観品質の要求が非常に厳しい輸送機器関係の成形品を多数手がけており、豊富な実績がございます。樹脂の真空成形・圧空成形・熱プレス成形・R曲げ加工から切削・溶接・組立のことなら三栄プラテックにお任せください。